Al2O3 Alumina Ceramic Substrate Pcb
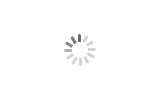
- MSJ/CS-004
- 96% alumina ceramic / aluminum nitride ceramic
- customized as per required specification
- 100 pcs
- high power electronic modules
Ceramic PCBs have much beter heat dissipation performance, current-carrying capacity, electrical insulation, thermal expansion coefficient than ordinary glass fiber PCB board. Unlike ordinary PCBs, which use adhesives to bond copper foil and substrate together, ceramic PCBs are produced by bonding the copper foil and ceramic substrate directly in a high temperature environment. Ceramic PCBs have strong bonding force, copper foil will not fall off, leading to high reliability and stable performance under high temperature and high humidity environment. Ceramic PCBs are widely used in high-power electronic modules, aerospace, military electronics and other products.
Any inquiry please email info@mascera-tec.com or call +86 13860446139
Product detail
Ceramic PCBs have much better heat dissipation performance, current-carrying capacity, electrical insulation, thermal expansion coefficient than ordinary glass fiber PCB board. Unlike ordinary PCBs, which use adhesives to bond copper foil and substrate together, ceramic PCBs are produced by bonding the copper foil and ceramic substrate directly in a high temperature environment. Ceramic PCBs have strong bonding force, copper foil will not fall off, leading to high reliability and stable performance under high temperature and high humidity environment. Ceramic PCBs are widely used in high-power electronic modules, aerospace, military electronics and other products.
Mascera is able to provide ceramic PCBs with alumina ceramic substrates and aluminum nitride substrates. Alumina ceramic is the most commonly used material for ceramic substrates which have good mechanical strength, heat resistance, impact resistance, electrical insulation and corrosion resistance. Because of the sufficient raw materials, affordable prices, and complete manufacturing and processing systems, alumina ceramic PCBs are the most cost-effective in the electronic packaging industry. Comparing with alumina ceramic substrate, aluminum nitride ceramic substrates have much higher thermal conductivity (7-10 times that of alumina ceramic), and its coefficient of thermal expansion (CTE) is close to that of silicon wafers, they are widely used in high-power semiconductor modules or large-scale integrated circuits.
Available Metallization Technology
Mascera develops two metallization technologies to produce ceramic PCB, one is DBC (direct bonding copper) and DPC (direct plating copper). DBC is suitable for circuits that line width and thickness are not critical, DPC is used to produce circuits that line size should be accurately controlled.
Item | DBC | DPC |
---|---|---|
Metallization Method | Direct Bonding Copper | Magnetron Sputtering + Electroplating |
Ceramic Substrate Type | 96% Al2O3 | 96% Al2O3 or AlN |
Thickness of Ceramic Substrates | 0.25mm / 0.38mm / 0.5mm /0.63mm / 0.8mm /1.0mm | 0.25mm / 0.38mm / 0.5mm /0.63mm / 0.8mm /1.0mm |
Maxim Size | 140 x 190mm | 140 x 190mm |
Metal Layer Material | Copper | Copper |
Metallization Surface | Single or Double | Single or Double |
Copper Layer Thickness | 70-300μm | >17.5μm |
Bonding Strength | >4.5N/mm | 3N/mm |
Minimum Line Width | 0.2mm | 0.1mm |
Minimum Line Spacing | 0.2mm | 0.1mm |
Surface Finish | OSP Ni Plating | OSP Immersion gold Immersion Ag Immersion Tin |
Feature of Ceramic PCB
Large current carrying capacity
Better heat dissipation performance, low thermal expansion coefficient, stable shape, not easy to deform and warp.
Good insulation, high pressure resistance, to ensure personal safety and equipment.
Strong bonding force, using bonding technology, the copper foil will not fall off.
High reliability, stable performance under high temperature and high humidity environment
Data Sheet for Ceramic Substrates
ITEM | UNIT | Technical Parameters | |
---|---|---|---|
Material Type | - | 96% AL2O3 Ceramic | AlN Ceramic |
Purity | % | 96 | 95 |
Color | ‐ | White | Light Grey |
Density | g/cm3 | ≥3.72 | ≥3.3 |
Warpage | - | ≤3‰*Length | ≤2‰*Length |
Flexural Strength | Mpa | ≥350 | ≥400 |
Thermal Conductivity (@RT) | W/m.k | >24 | ≥170 |
Coefficient of Thermal Expansion(20-800℃) | 10‐6mm/℃ | 6-8 | 4-6 |
Max working temperature | ℃ | 1650 | 900 |
Dielectric Constant(1MHz,@RT) | - | 9-10 | 8-10 |
Dielectric Loss(1MHz,@RT) | - | ≤0.0003 | ≤0.0003 |
Dielectric Strength | KV/mm | 17 | 17 |
Volume Resistivity | Ω.cm | ≥1014 | ≥1014 |
Typical Application of Ceramic PCB
High-power power electronic modules, solar panel components, etc.
High frequency switching power supply, solid state relay
Automotive electronics, aerospace, military electronics
High-power LED lighting products
Communication antenna, car ignition
Packing & Shipment
Package type | carton box with foam protection |
Payment terms | TT / Western Union / Paypal 50% payment in advanced and 50% before shipment |
Loading port | Xiamen, China |
Shipping way | By sea / air / door-to-door express |
Why Choose Us
10+ years experience in technical ceramics manufacturing and R&D
ISO9001:2015 certificated quality control management system
Different types of ceramic materials are provided for your different applications
Products have been exported to 40+ countries and have good reputation from our customers
MOQ is low, both prototype and bulk order will keep high quality
Any of your inquiries or questions will be responded no longer than 24 hours
Rigorous production plan to ensure on-time delivery